How Warehouse Investment and Management Can Combat Material Shortages and Escalations
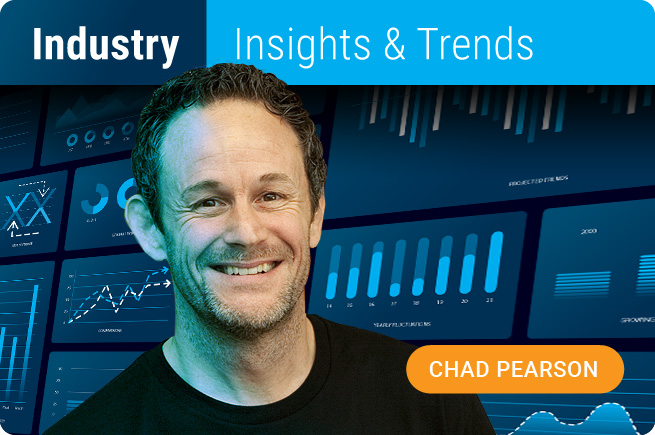
Amidst the current global economic landscape, material shortages and cost escalations have become increasingly prevalent. Material shortages can result in lost sales, production delays, and customer dissatisfaction. Escalations, on the other hand, can lead to increased costs and reduced profitability.
In this blog, we’ll explore how warehouse investment and management can combat these issues.
Investing in Warehouse Infrastructure
By building or expanding warehouse facilities, businesses can store and manage more inventory, reducing their reliance on just-in-time (JIT) supply chains. JIT systems rely on a tight inventory control system, where raw materials and components are delivered just as they are needed without having to store excess inventory. However, this system is vulnerable to disruptions in the supply chain. By investing in warehouse infrastructure, businesses can build inventory buffers that can be used to address material shortages and escalating prices.
Implementing Warehouse Management Systems
Warehouse management systems (WMS) software helps businesses manage their inventory levels and track the movement of materials in real-time. This technology enables businesses to optimize their warehouse operations, reducing inventory carrying costs and minimizing the risk of stockouts. By implementing WMS, businesses can also reduce the time it takes to find and pick materials, increasing efficiency and reducing the likelihood of delays.
Embracing Automation
Warehouse automation technologies such as robotics and automated guided vehicles (AGVs) can help businesses increase efficiency, reduce labour costs, and reduce the risk of human error.
For instance, robotics can help businesses manage inventory levels and optimize warehouse space, while AGVs can transport materials around the warehouse more efficiently. By embracing automation technologies, businesses can reduce the time it takes to manage inventory and the likelihood of stockouts.
Improve Visibility
With the help of technology such as IoT sensors, RFID tags, and GPS tracking, businesses can gain real-time visibility into their supply networks, from raw material acquisition to finished product delivery. This can help businesses identify potential bottlenecks, optimize delivery routes, monitor inventory levels, and make informed decisions to prevent stockouts and delays.
Build Strong Partnership
By establishing a strong relationship with suppliers and distributors based on trust and transparency, businesses can work collaboratively to identify potential risks and mitigate supply chain disruptions. This involves streamlining communication, establishing effective forecasting methods, and developing contingency plans in case of emergencies.
Implement Sustainable Practices
With the growing awareness of environmental concerns, consumers see businesses that prioritize sustainability as being socially responsible and environmentally conscious. Incorporating sustainable practices into your warehouse operations can help reduce costs, improve efficiency and gain customer loyalty. This includes implementing energy-efficient lighting, recycling programs, reducing packaging, and optimizing the logistics network to reduce carbon footprint.
Plan and Forecast for Future Demand
Accurately forecasting future demand for your product will allow you to manage inventory more effectively. You’ll be able to ensure you have enough inventory to meet customer demands while avoiding costly overstocking. Carrying too much inventory for too long can lead to material waste and reduced profits for your business. You should regularly review historical data to identify trends and plan for upcoming peaks and valleys in demand.
Investing in warehouses can provide a buffer between suppliers and construction sites, reducing the risk of shortages and stabilizing prices. Effective warehouse management involves monitoring inventory levels, managing logistics, and optimizing space utilization. Investing in technology can also help warehouses operate more efficiently. By implementing these measures, the construction industry can overcome material shortages and price escalations, enabling it to continue to provide essential infrastructure.
*Brought to you by Plexxis Software: Offering software solutions for the construction industry that integrates cloud, mobile and on-premise software to improve and enhance team performance.